Hydrant Guard Success Story: Las Virgenes Municipal Water District
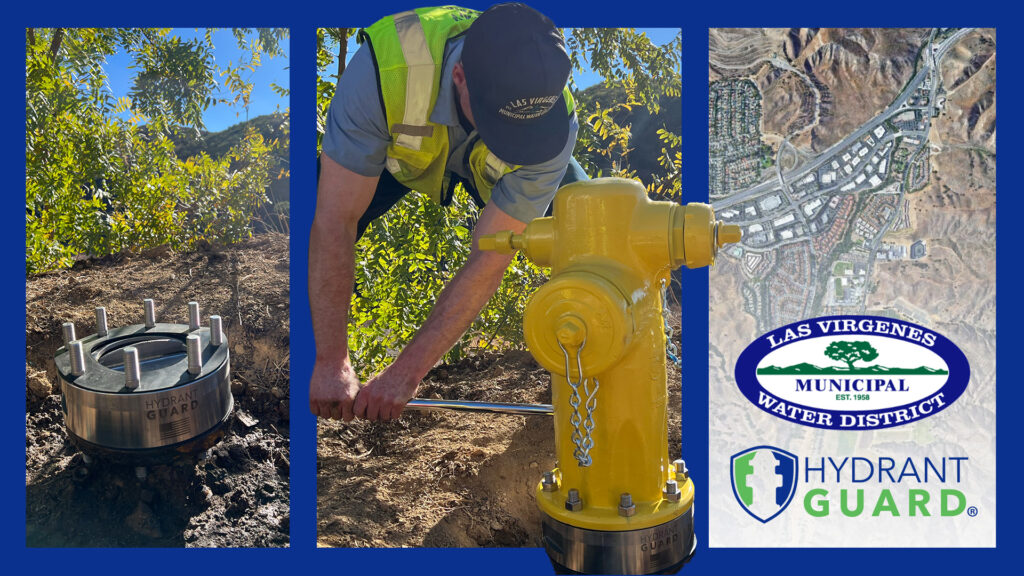
When Andy Arenas and his team heard about Hydrant Guard, they were skeptical at first: “we usually find ways to cut stuff up on how it won’t work for our type of usage, whether it’s for pressurizing, installation…we can usually figure out a reason why we can’t use it.”
Andy’s team had just taken over the hydrant program at the Las Virgenes Municipal Water District, which meant all things hydrant related, maintenance and installation, now fell under his purview. “Once it got to me, I revamped our whole hydrant program. We’re going to replace a minimum of 100 hydrants a year.” Andy and his team wanted to maximize impact on these new installations and prevent future water loss. LVMWD’s unique terrain makes shears particularly troublesome, with hydrants located in hard-to-reach, traffic-jammed canyons. At many junctures their service area flanks the 101 Freeway, so a local shear gone haywire can cause large-scale disruptions.
Not long before Andy first came across Hydrant Guard, LVMWD dealt with a mega-shear event, losing a million gallons of non-revenue water, flooding private property and triggering damage claims. The costly incident made one thing clear: they would need a solution to prevent disasters like this in the future.
Around that time, Jesse Anderson, Hydrant Guard’s sales rep, introduced the team to Hydrant Guard’s stainless steel check valves. “Jesse reached out and told us about this device that was going to change the water industry…we were willing to listen, and he presented us a product that was close to being there.” Still, Andy wasn’t sure Hydrant Guard would solve their district’s specific challenges. He had used other check valves in the past and had various issues that made them non-starters. Some required concrete pads, others needed to be raised or lowered to very specific levels. Others simply did not perform: “We’ve had some that just broke off and go wide open on shears anyway. They just weren’t built the way we wanted them to be”.
Right away Hydrant Guard struck Andy’s team as different: “Between all of us in this group, we’ve seen quite a few pieces of equipment. We liked the idea that it was solid and just started from a big chunk of stainless steel. You might have to change out a butterfly or a spring, but you’re not losing the vessel: your big chunk of stainless isn’t going to change.”
Encouraged by Hydrant Guard’s design and construction, they started looking more closely at the specifics, dialing in to find the product’s weaknesses:
Q: if there’s a small service leak, can we highline the hydrant without cutting off water flow (we’ve had problems with this with other check valves in the past)?
A: Yes, highlining will not affect flow.
Q: If there’s a partial, non-structural hit, will the spring doors close?
A: No, the water keeps flowing as it should. The valve doors only shut if the hydrant is sheared.
Q: Will the breakaway bolts shear on impact, spring the valve doors shut and keep the hydrant intact?
A: Yes. Hydrant Guard CNC machines breakaway bolts in-house to ensure consistency. They’re carefully designed to break on impact without causing damage to connected infrastructure or twisting the base of the hydrant.
The fact that Jesse answered their questions thoughtfully and took their feedback in stride boosted LVMWD’s confidence that Hydrant Guard had real potential to solve their shear problems. As Andy recalls, “It really helps when you have someone like Jesse who’s willing to give you all the information and is willing to answer your questions. If he can’t answer, he goes, ‘Let me go talk to my guys.’ It’s really nice to know that this is a guy who listens to your feedback, because making yourself accessible to the water industry is major.”
The next step was a field test. The Hydrant Guard team brought valves to LVMWD and allowed the hydrant team to install them to their own system. Long story short, the trial was a resounding success.
After a successful field test, the LVMWD hydrant team had all the data they needed to justify the addition of HG to their spec and to make a case for including it on many of their new installations. “At the end of the day [Hydrant Guard] is simple in the way that it works, but it’s ingenious in the way it’s going to save water. That’s why I’m so adamant about putting this into our system.”
A further consideration for adding Hydrant Guard to the spec was the potential cost savings. Since Hydrant Guard’s installation is so easy, the majority of the costs are up-front in the actual equipment. All you need after that are two operators and hand tools for a successful install. When comparing that to the manpower and resources required for a new hydrant installation, it’s a small fraction of the cost. Based on Andy’s experience, just one prevented shear easily covers the cost of multiple HG installs.
In his incident report under Total Water Loss, Andy wrote “5 gallons.”
The value of the new check valves soon became very apparent in real-world terms. The same hydrant that unleashed the million-gallon geyser was struck again. Only this time, instead of hemorrhaging water, Hydrant Guard effectively sealed the water main below the sheared hydrant. When Andy arrived on the scene of the shear, he found nothing more than signal spray. In his incident report under Total Water Loss, Andy wrote “5 gallons.”
Among everything he’s accomplished since taking over the hydrant team at LVMWD, Andy is happy to finally have a solution to the problem of hydrant shears. “A Hydrant Guard can save a million gallons of water,” he says. “They’re paying for themselves.”
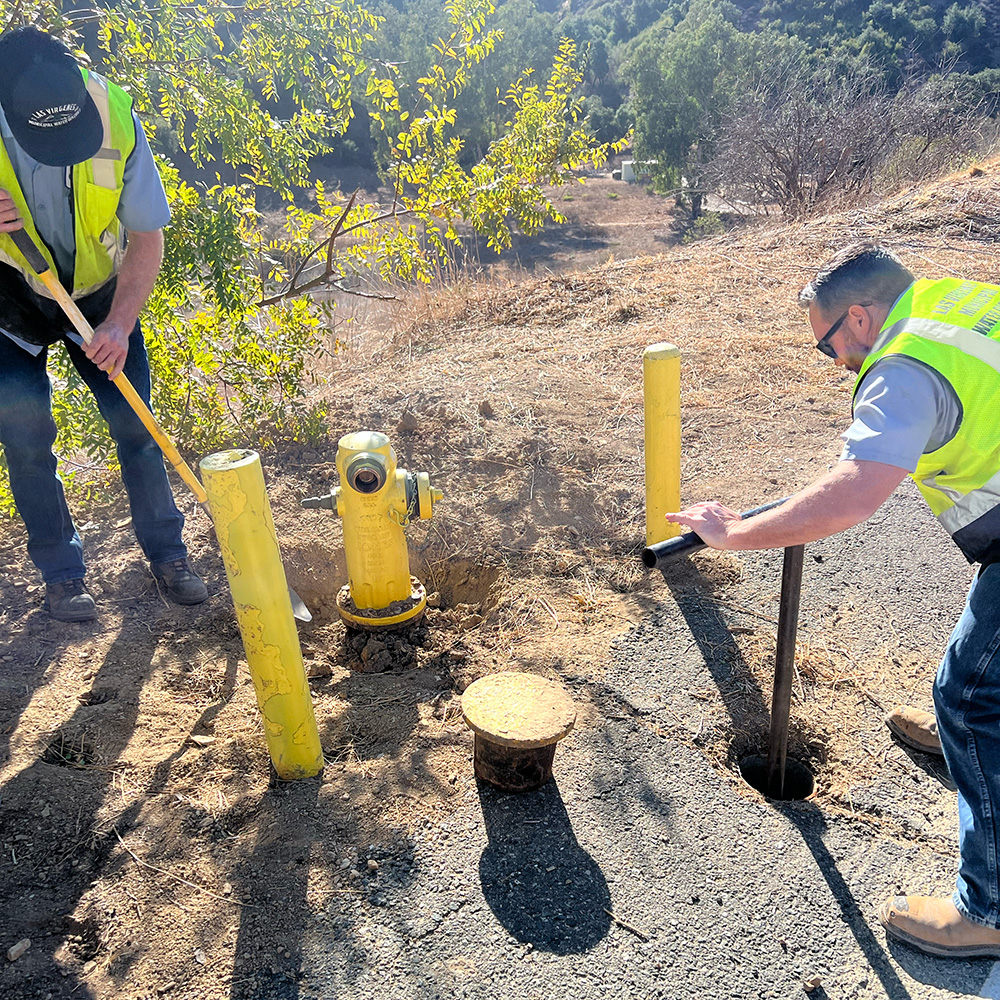
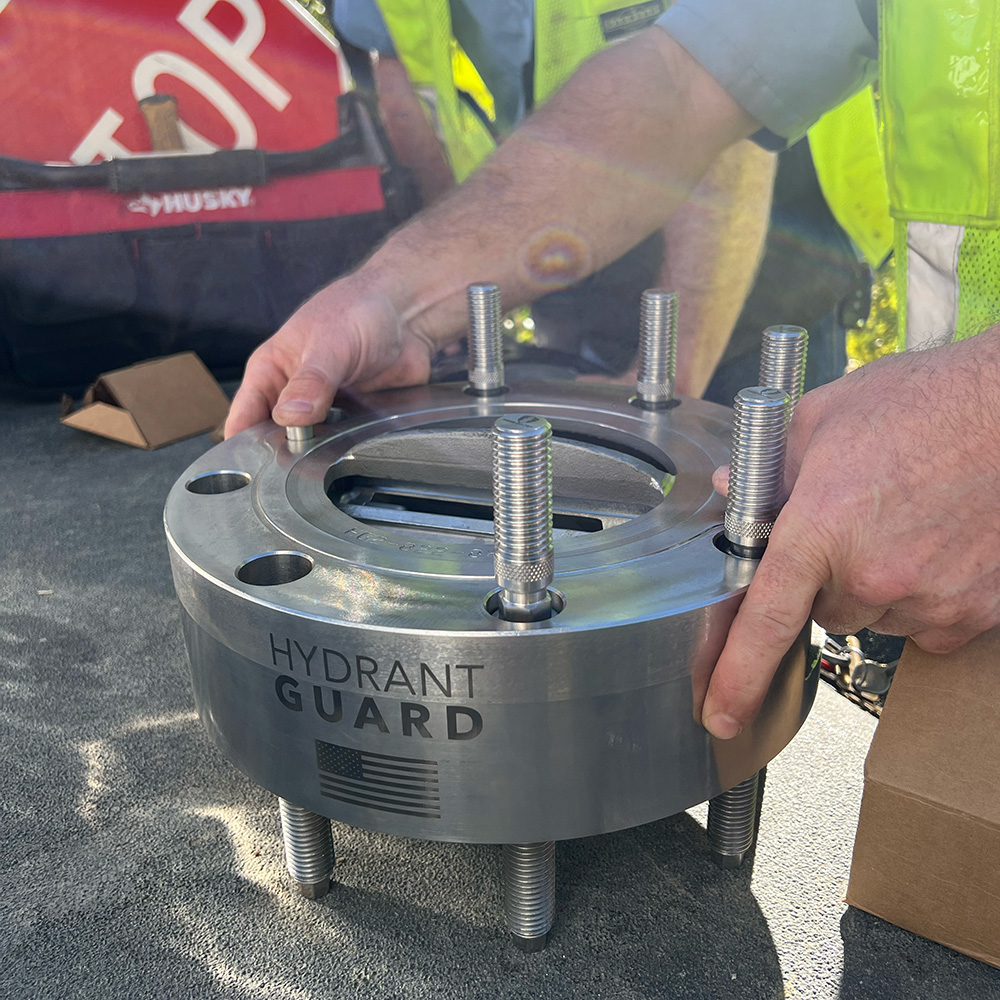
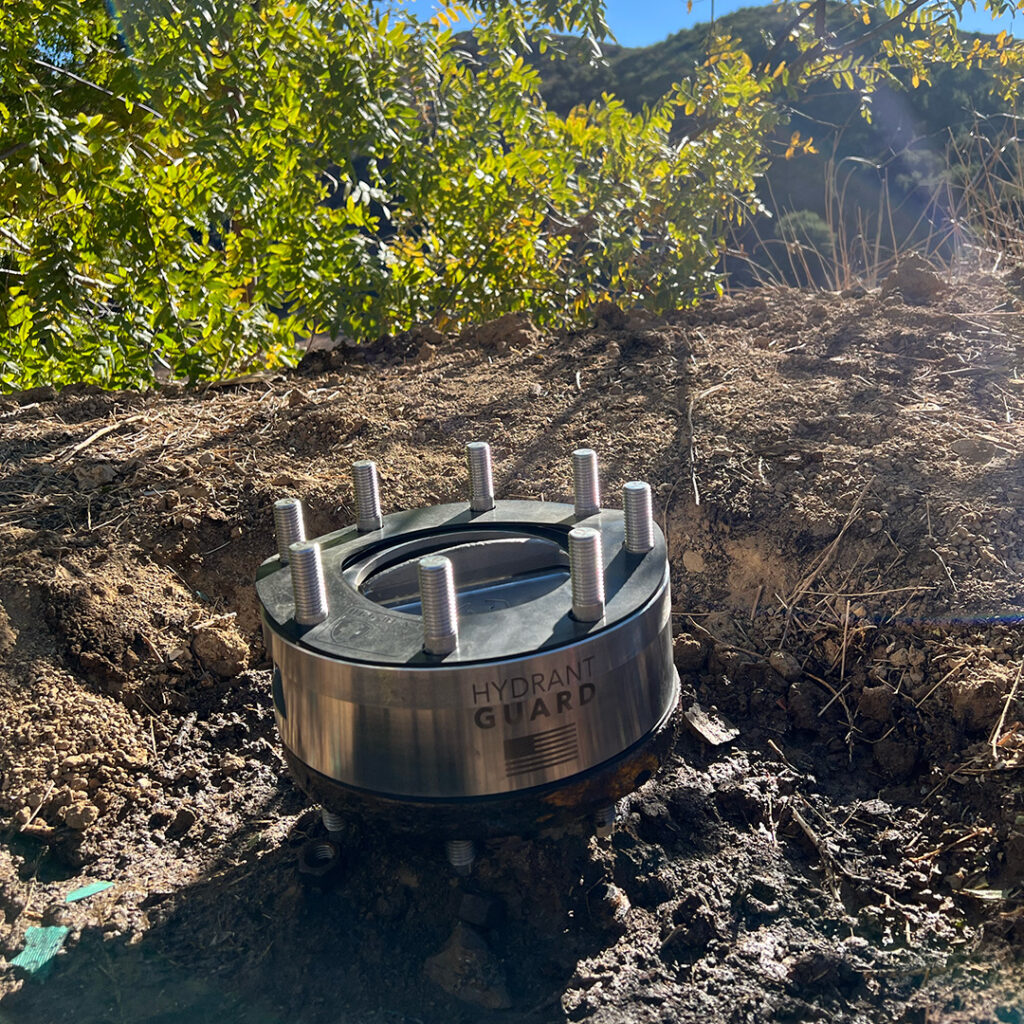
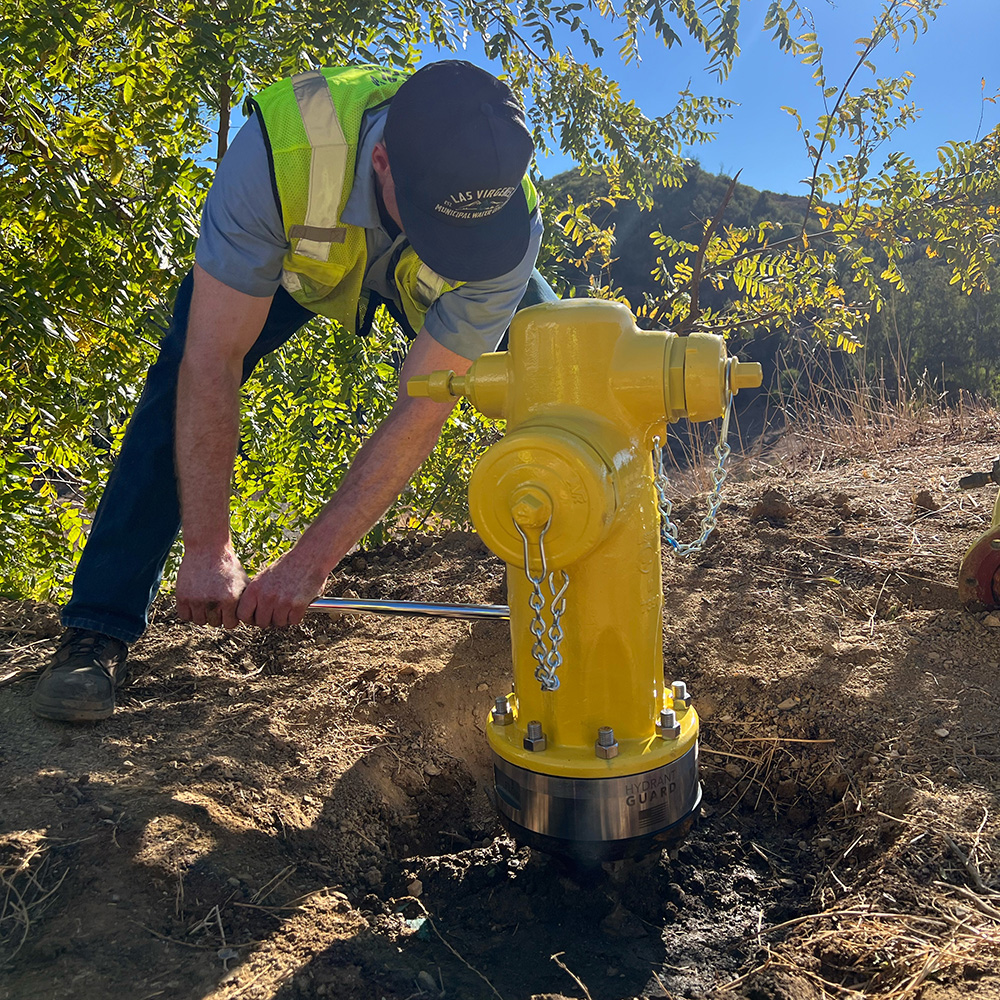
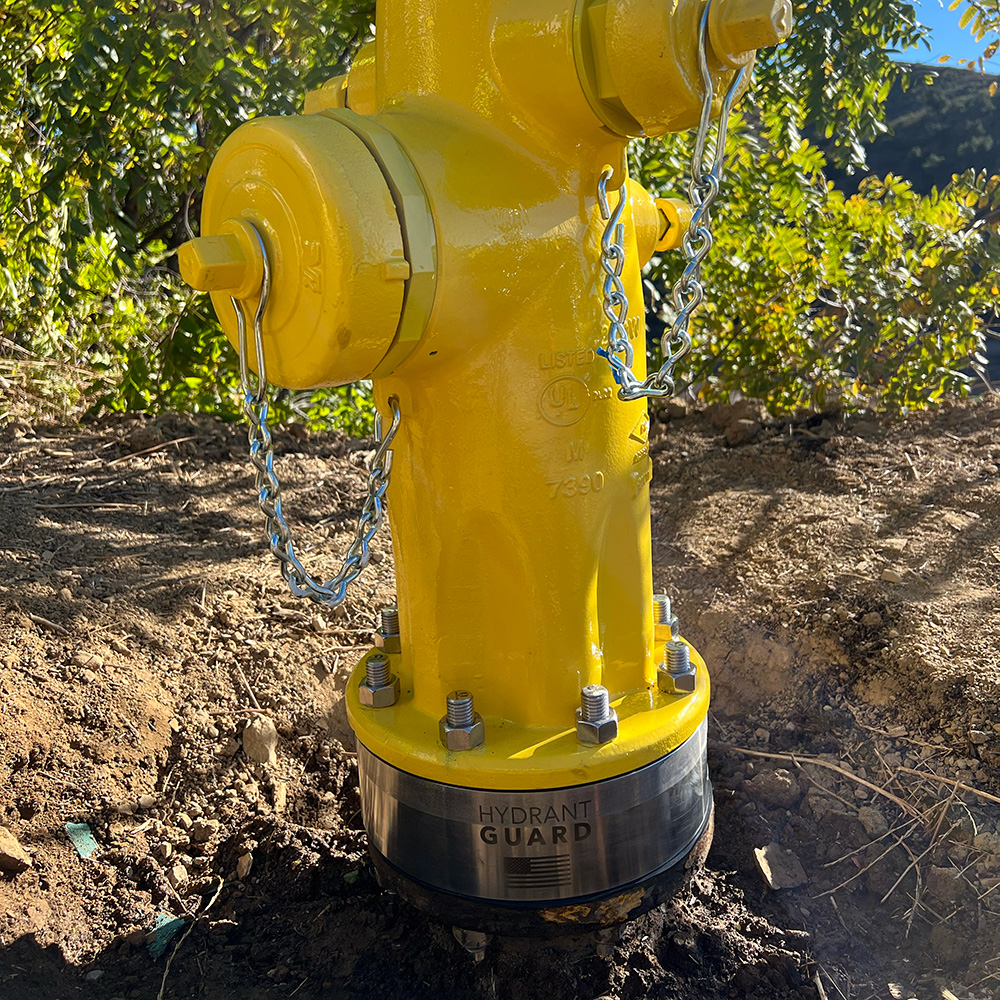
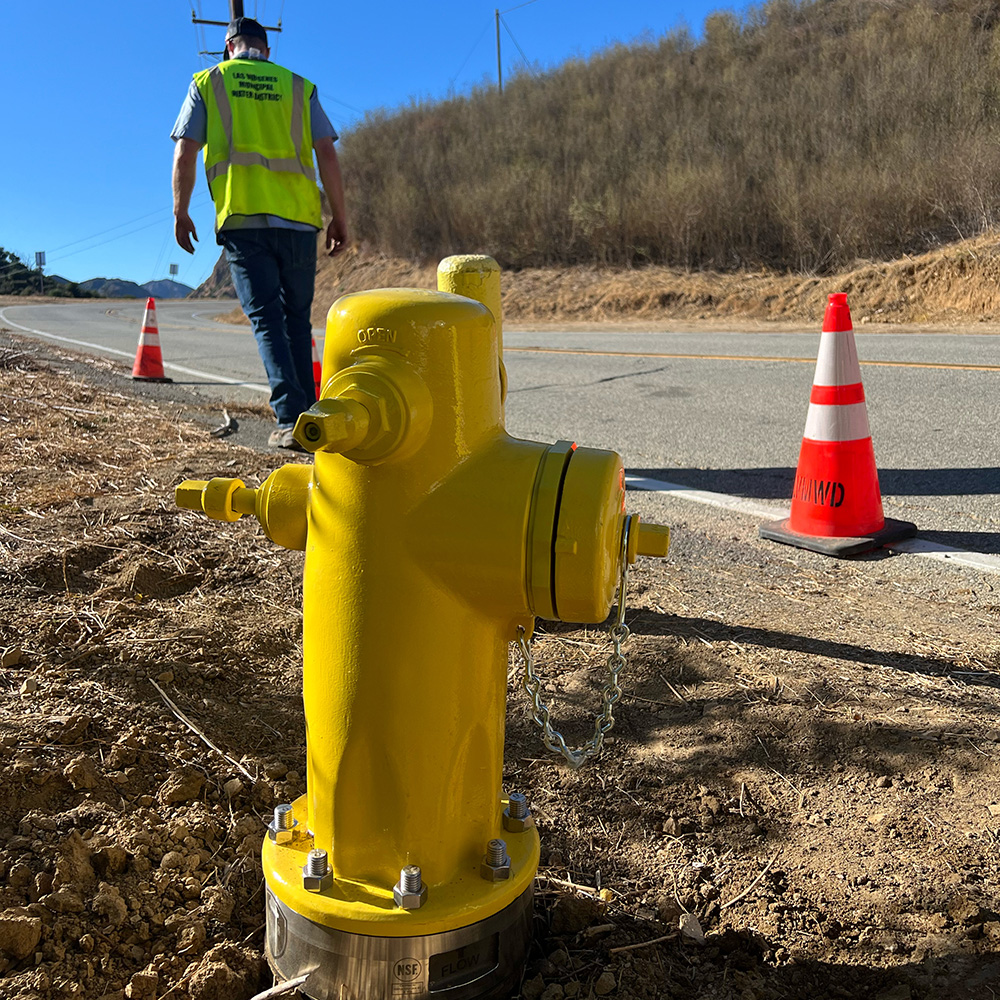